Printing your own mechanical parts or toys is really easy, not to mention fun, using a 3-D printer. But things get a bit trickier when you want to print the kind of parts that go into a car or airplane. Metal is a lot more complex to work with inside a 3D printer than polymers like ABS – the kind of film roles that get melted layer by layer to form a part of your liking once it cools down. Engineers at General Electric just demonstrated, however, that in practice it’s not that complicated to print parts out of metal alloys as it sounds. The team used additive technology to build a fully functional jet engine, then test powered it to 33,000 RPMs. The company is already using 3-D printed fuel nozzles in its next-generation aircraft engines, slated to role out in 2016.
“We wanted to see if we could build a little engine that runs almost entirely out of additive manufacturing parts,” says one of the engineers. “This was a fun side project.”
The GE team planned, designed and built the engine over the course of a couple of years, in their spare time off from their main projects. In their lab at the GE Aviation’s Additive Development Center outside Cincinnati, they employed a next-generation technique that can make complex 3D structures by melting metal powder layer upon layer.
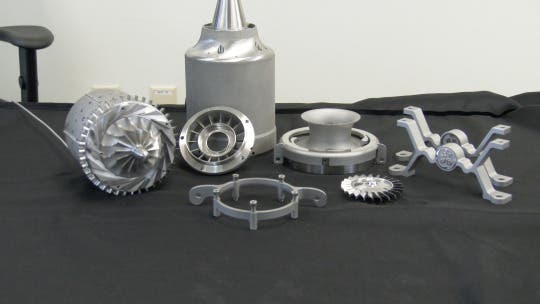
An airplane’s jet engine is of massive complexity, costs millions of dollars and involves hundreds of man hours to assemble. Since this was their first test run, the team tackled a much simpler design. They found the plans for an engine typically used in remote controlled model airplanes and adapted it for 3D printing. Each part was printed, polished then put in assembly; the final product measured a foot long by about eight inches tall. They then mounted some control sensors, like those that measure exhaust gases, and put the engine inside a test cell that’s typically used to gauge performance for large-scale engines. They fired it up to 33,000 RPMs, showing that the part doesn’t break. The General Electric press release doesn’t specify however how many cycles the mini jet engine was subjected to.
Parts are typically made by casting or through traditional machine methods that cut parts out of larger pieces. The GE technique uses a laser and powdered metal to fuse new parts, layer by layer. The resulting parts can be made using much more complex geometries and different alloys unavailable otherwise. It also cuts material waste, but not necessarily expenses per part since this is still a fledgling technology.
“There are really a lot of benefits to building things through additive,” says Matt Benvie, spokesman for GE Aviation. “You get speed because there’s less need for tooling and you go right from a model or idea to making a part. You can also get geometries that just can’t be made any other way.”
Was this helpful?